Introduction
In the electrifying world of Battery Management Systems (BMS), choosing between MOSFETs (Metal-Oxide-Semiconductor Field-Effect Transistors) and contactors can make or break your battery system’s performance. Buckle up as we dive into this comprehensive technical comparison, helping you understand the nuances and make an informed decision for your products and applications.
What’s a BMS, Anyway?
A Battery Management System (BMS) is essential in any battery-powered system, ensuring optimal operation and safety. Its primary functions include:
- Monitoring: Continuously measuring battery parameters such as voltage, current, and temperature.
- Balancing: Ensuring equal charge levels across all cells to prevent imbalances that can reduce battery life.
- Protection: Safeguarding against overcharging, over-discharging, overcurrent, and overheating.
- Diagnostics: Providing real-time data and alerts for maintenance and troubleshooting.
The BMS also manages power delivery from the battery by controlling the output switching mechanism. This can be achieved through MOSFETs, controlled via digital signals to a gate driver, or through contactors, controlled via coil excitation.
MOSFET-Based BMS
Overview
MOSFETs are semiconductor devices that function as electronic switches, controlling the flow of current in a circuit. In BMS applications, MOSFETs manage the connection between battery cells and the load or charger.
Advantages
- Low On-Resistance (R<sub>DS(on)</sub>): MOSFETs have significantly lower on-resistance compared to contactors, resulting in minimal power losses and optimal thermal performance of the BMS. This is crucial for applications where energy efficiency is paramount.
- High Switching Speed: MOSFETs can switch on and off in nanoseconds, enabling high-frequency operation. This ensures an effective and fast response for short circuit protection, which is critical for battery safety.
- Economical: Due to their mass production and well-established supply chain, MOSFETs are a cost-effective choice, making them readily available and affordable for various applications.
Challenges
- Cost at High Power Ratings: While MOSFETs are cost-effective at lower voltages, their cost increases significantly for higher power applications due to the need for multiple devices and complex gate drive circuits.
- Complex Design for High power applications with compact BMS requirement: High-power applications require a large number of MOSFETs, which increases the space needed on a single board and complicates both the MOSFET control system and the overall design and integration process.
- Thermal Management: MOSFETs depend on effective heat sinks for thermal mechanical integration to dissipate the heat generated during operation. This adds to the complexity and cost of the system.
Applications
MOSFET-based BMS is compact and ideal for high-efficiency, fast-switching, and precise control applications, such as:
- Electric Vehicles (EVs)
- Renewable Energy Storage Systems
- Portable Electronics
- Drones
Contactor-Based BMS
Overview
Contactors are the sturdy workhorses of the BMS realm. These electromechanical relays physically connect or disconnect electrical circuits, making them perfect for high-power applications.
Advantages
- High Current Handling: Contactors can manage very high currents (hundreds to thousands of amps) without significant heat generation or efficiency loss, making them suitable for high-power applications.
- Complete Electrical Isolation: When open, contractors provide complete electrical isolation, enhancing safety in high-voltage systems.
- Cost Efficient: For applications above certain voltage thresholds (typically around 72V or above), contactors become more cost-effective compared to MOSFETs due to the reduced need for parallel devices and complex gate drives.
- Durability: Contactors are known for their mechanical durability and long lifespan, even in harsh environments.
Challenges
- Slower Switching Speed: Contactors have slower switching speeds compared to MOSFETs, limiting their use in applications requiring rapid switching, which means slower response during safety critical conditions like short circuit where fastest response for protection is expected.
- Size and Weight: Contactors are generally larger and heavier than MOSFETs, which can be a disadvantage in space-constrained applications.
- Mechanical Wear and Tear: Being mechanical devices, contactors are subject to wear and tear, which can lead to maintenance issues over time. Contactor welding issues can arise over long periods of high-power operation. Welded contactors expose the battery to various failures, including short circuits, overcharging, undercharging, thermal runaway, and a compromised ability of the BMS to protect the battery.
Applications
Contactor-based BMS are perfect for high current handling and robust applications, such as:
- Industrial Energy Storage Systems
- Backup Power Systems
- Heavy-Duty Electric Vehicles (buses, trucks, and more)
- 3-wheelers (Delivery trucks)
- 4-wheelers (Cars, trucks, and more)
- Renewable Energy Installations
Cost Analysis: When Do Contactors Become the Budget-Friendly Choice?
Contactors shine in high voltage and high current applications. For systems running at 72V or above and requiring continuous currents over 100A, contactors are the more economical option. Here’s why:
- Reduced Number of Devices: High voltage MOSFETs are costly, and using many in parallel to handle high currents ramps up the price. Contactors can manage high currents without needing multiple devices.
- Simplified Gate Drive: MOSFET gate drive circuits for high voltages are complex and expensive. Contactors don’t need such intricate drives, cutting overall costs.
- Longevity and Maintenance: Despite higher initial costs, contactors’ mechanical durability means lower long-term maintenance costs compared to MOSFETs.
Maxwell’s BMS Solutions
At Maxwell, we’ve got you covered with both MOSFET and contactor-based BMS solutions. Whether you need the fast-switching prowess of MOSFETs or the robust power handling of contactors, our innovative designs ensure reliable, efficient, and safe battery management. Check out our product range and find the perfect solution for your needs.
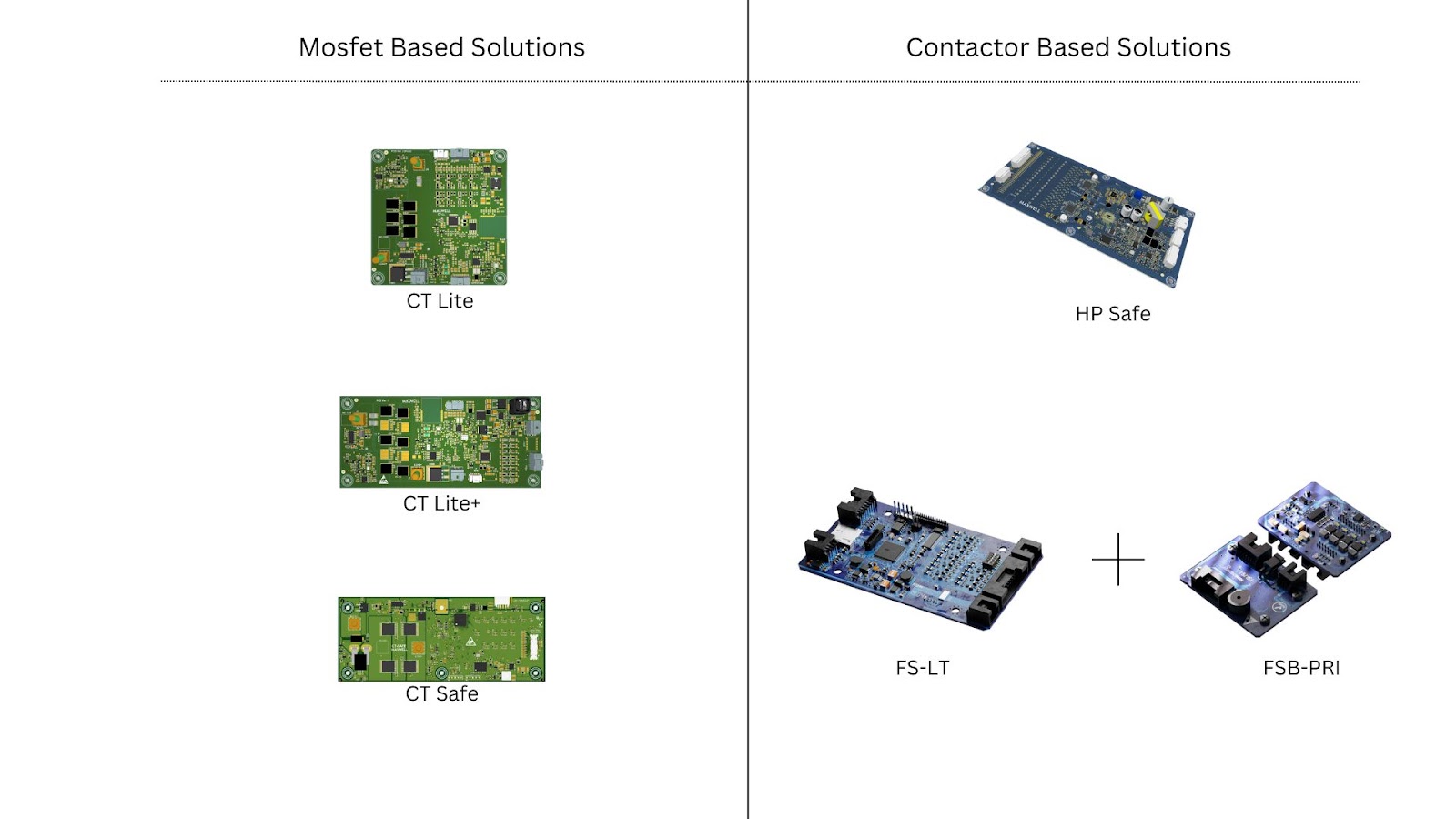
Conclusion: Making the Right Choice
Choosing between MOSFET and contactor-based BMS depends on your specific application requirements. Here's a quick summary to guide your decision:
- For high efficiency, fast switching, and compact size requirements with advanced control: opt for MOSFET-based BMS.
- For high current handling, robustness, and cost efficiency at high voltages: Choose contactor-based BMS.
Both technologies have their unique advantages and challenges. Understanding these nuances allows you to select the best BMS technology to optimize the performance, safety, and cost-efficiency of your battery-powered systems.