How ION’s platform helped design, power and deploy an all electric excavator to operate in extremely cold temperatures
ION partnered with a leading European battery pack maker to enable its customer –A European construction equipment maker – to deploy their first, fully electric excavator.
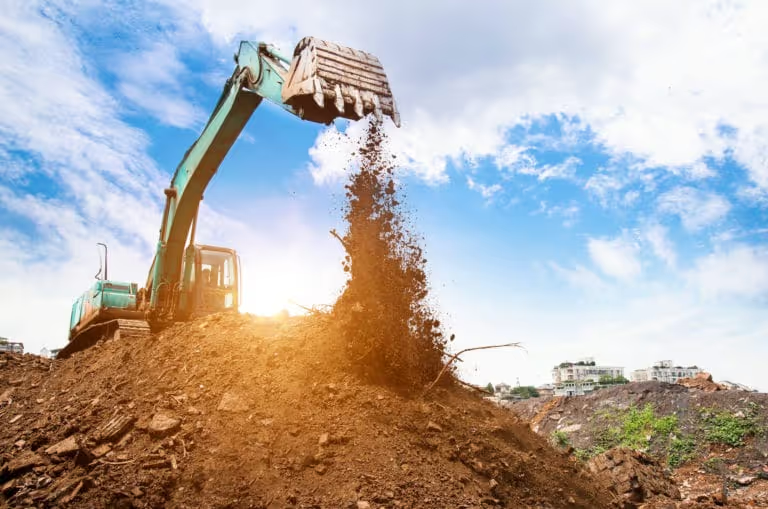
Image caption goes here
About customer
An established European leader in the battery pack manufacturing space, who undertakes the design, manufacturing, and development of batteries and power supply systems. Our partner has spent over 30 years in powering customers across a diverse range of industries in multiple countries, with advanced R&D capabilities, production of rechargeable and non- rechargeable batteries, highly efficient equipment types, mechanical components, and electronic systems.
A reputed and reliable European construction equipment and worksite technology builder, that has been enabling companies worldwide for over a century with high-end applications and innovations. They deliver a wide range of construction equipment that includes – cranes, excavators, forklifts, etc. They even undertake projects that require custom-design construction products, services, and solutions.
Outcome we delivered
100,000+
Units Deployed
85+
Customers
15+
Countries
Challenge for Maxwell
As the electrification of transport rapidly spread to multiple other industries, the customer felt the need to build sustainable, zero-emission construction machines that could replace the diesel engine completely. They envisioned designing and deploying a range of compact, fully rechargeable clean energy construction equipment. The objectives were to deliver zero exhaust emissions, reduce the noise, pollution, and maintenance requirement, improve efficiency and reduce costs.
Their challenge was to undertake their first electrification project for construction equipment, that would operate under extremely low temperatures (-20 degrees). The success of this project was critical, considering the investment in terms of time and cost. After numerous discussions held internally, they set out to find a partner who could help them power their first, fully electric excavator, within a year.
The powertrain that was needed to build electric construction equipment would significantlyvary from that of a passenger car! Given the challenges and complications of this project, the customer was looking for a partner with the right experience, expertise, and advanced technological capabilities.
After having met with multiple potential partners, who were failing to meet their expectations within the given timelines, they approached ION Energy’s trusted partner who had a strong foundation in developing technology and electronic systems, R&D, and rechargeable battery production. The customer felt confident about setting out on the enormous endeavor of producing their first, commercially viable, electrically powered excavator.
Our partner analyzed multiple complexities and aspects of battery management in low temperatures. The challenge they faced was to identify a smart battery management system provider who would enable a highly scalable and efficient Master and Slave architecture for batteries manufactured by the partner.
They actively started meeting BMS providers across the world who could bring the engineering and technological capability to help materialize this project. Because of the immense growth potential, they were looking for a versatile and reliable partner to help them with the design, control, and deployment of smart BMS for their customer.
They discussed the project with the team at ION and found the team focused on building technologies that essentially improve the life and performance of lithium-ion batteries. They chose ION because of the team’s commitment to building innovative business models, BMS’s typical capabilities like state-of-charge and state-of-health monitoring and cell balancing, coupled with connectivity and data logging, and access to ION’s analytics platform.
Our Solution
ION Energy’s advanced battery management and intelligence platform is designed with accelerated engineering capabilities and artificial intelligence-driven predictive analytics software. OEMs and battery pack makers in markets across the US, Europe and India choose ION’s integrated battery management solution for our reliability, transparency, and commitment towards customer success.
Our technological expertise, in-house hardware, and firmware development capabilities, real-time data visualization, and customization were the key determining factors that helped ION emerge as the ideal solution provider.
ION kickstarted the project with instant activation support. A dedicated engineering team started by visiting the customer site to ensure a smooth integration and testing process.
The team began implementing all software functionalities needed to meet the customer’s timelines. The hardware was customized to meet the customer’s present and future electrical and mechanical specifications.
At extremely cold temperatures, lithium-ion batteries retain just 12% of their capacity. Hence, ION developed and implemented a unique Battery Heater Management system to manage safe battery operations at extremely low temperatures – up to -40 degrees celsius. The system powers up the heaters using onboard chargers and brings up the battery to an acceptable temperature before turning it on.
Our battery intelligence platform gave them adequate control, simplified data analytics, remote diagnostics, and preventative maintenance services.
ION successfully enabled the construction equipment maker to electrify its first excavator and continues to design platform solutions for the customer. ION has ensured a minimum business of $1.5 million for the partner in 2019 that would increase to $100 million in the upcoming years.
BMS Master-Slave Architecture
While there are multiple ways to implement a battery management system, to successfully tackle the partner’s master-slave architecture challenge, ION chose the Daisy chain formation method in the existing FS-LT BMS and later on built the FS-XT BMS, that is designed for High Voltage battery systems that better suit the requirement.
FS-XT is a distributed Battery Management system designed for High Voltage battery systems. Its premium features are suitable for automotive and storage applications like support for the insulation monitoring device, system interlock monitoring, contactor weld detection and system communication with isolated CAN.
It uses multiple smaller battery modules connected in series or parallel. The compact yet robust FS-XT master can connect up to 40 slave modules/combinations. Each Slave unit can monitor from 6 to 18 cells in series.
The slave units communicate with the Master over the state of the art isoSPI protocol without the need for a processor. The slave takes its power from the cell it is monitoring and a two-wire isolated SPI. The Master unit runs advanced SOC and SOH algorithms. It also comes with premium safety features suitable for automotive and storage applications like support for the insulation monitoring device, system interlock monitoring, contactor weld detection and system communication with isolated CAN. The daisy chain formation is highly scalable, efficient and cost-effective. Since the battery is huge, it becomes important to have a distributed architecture within the Battery Pack. The daisy chain makes the distributed architecture, while the master controls it.
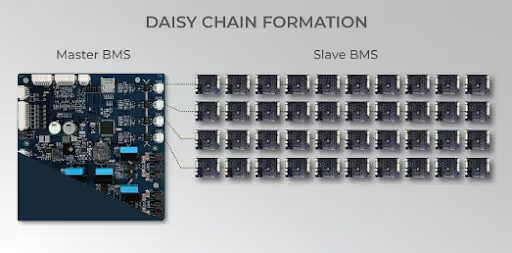
Product deployed
Advanced Battery Management System & Intelligence Platform
Using our battery intelligence platform – Edison, the partner was able to visualize, predict, and make sense of the battery data to improve the battery life. The real-time analytics helped the team use over 170configuration parameters, identify issues and troubleshoot problems beforehand in the design, testing, and prototyping phase. Edison is an AI-powered battery lifecycle management platform that leverages battery specifications, environmental conditions, application context, and usage patterns to accurately gauge the current state of health, predict the end of life, estimate the commercial value and optimize for the second life of the batteries.
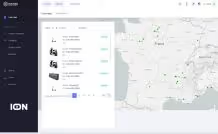
The features of the Master in this architecture:
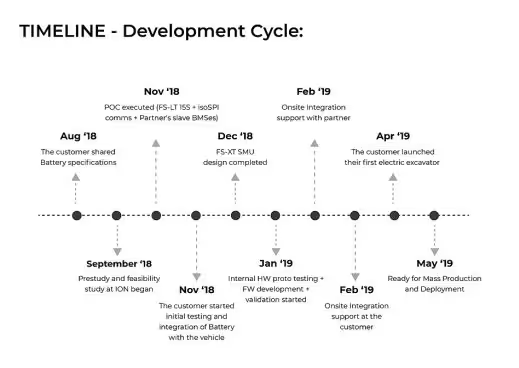
Companion applications
Lens
ION Lens is used to remotelyinterface, activate and connect tothe BMS. It transfers the batterydata to Edison via Bluetooth orWifi. ION Lens showcases the overall batterystatus including parameters like:
Trace
ION Trace is a supply chainapplication that can be usedto add a new component inyour inventory, test, assem-ble, ship, and associate with a BMS. IONTrace lets the user scan and view thefollowing component details:
What they say about us
We searched for the best components and technology in the world for our electric scooter, which has been developed to fulfill the highest expectations of the premium urban mobility customer in large European metropolitan areas. Maxwell, with its smart BMS solution, has proven to be the perfect partner for us, and gives us the quality and scalability we need for our growth strategy.
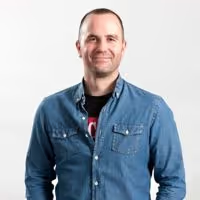
Íñigo Raventós Basagoiti
CEO - Ray Electric Motors